镀铝锌彩涂板是彩涂建筑板中的高端产品,外观靓丽、用途广泛。但镀铝锌彩涂板生产中,除了具有高强的防腐性能之外,当然也有一定的缺陷,但是都是可以通过彩涂板机组或是工艺改变的,其表面易产生爆孔、气泡等缺陷,严重影响了彩涂线的连续生产和镀铝锌彩涂板的表面质量,造成成材率低下,需要分析。
原因分析:
1、镀层化学特性差异
由于锌铝合金镀层结晶时间长、枝晶发达,三叉结晶处属于后凝固区域,*形成疏松和孔洞。疏松和孔洞形成的凹陷缺陷的存在也导致空气滞留。在涂料涂装固化过程中,空气体积膨胀,穿过透气性好的底漆,使面漆破损,造成爆孔缺陷。
2、镀层热物性差异
镀铝锌合金镀层的热辐射系数为0.86,较镀锌层的0.45高出很多,以镀铝锌板作为基板时,镀铝锌层使其表面的涂层快速升温、快速固化,造成涂料中的**溶剂不能以合理的速度及时散发,从而造成爆孔、气泡缺陷,在底漆较厚时更易出现爆孔缺陷。
3、缺陷的影响
镀铝锌彩涂基板生产时,校正辊振动、液面波动产生使其横向周期分布的色差,是造成爆孔缺陷产生的原因。镀锌铝表面锌花不均,所形成的晶界间存有凹陷,凹陷内有残留空气,在面漆固化过程中空气冲破漆膜发生爆孔。
因此,控制措施为:
1、提高镀层均匀性
应按标准锌花样板,检查锌花大型,同时及时调整。提高三辊六臂装配质量,优化校正辊材质和尺寸,减少校正辊振动和锌锅液面波动幅度;保证镀铝锌彩涂基板表面质量达到FB以上。
2、改进表层粗糙度
为避免彩涂生产时出现爆孔缺陷,镀铝锌生产线生产彩涂基板时使用大粗糙度工作辊,轧辊粗糙度控制在4.0±0.3μm,进而改善基板粗糙度。
3、优化彩涂固化工艺
针对镀铝锌合金基板和涂料的特性,改进涂装固化曲线,调整机组工艺速度,使涂料在固化中保证合金层孔洞中的气孔和涂料中稀释剂充分逸出,有效控制溶剂挥发速度,防止溶剂沸腾蒸发。将直线式固化温度曲线修改成阶梯式固化温度曲线,保证涂料的PMT,降低机组工艺速度15%,面漆的固化时间,保证涂装工艺温度稳定,适当降低涂装粘度,改善镀铝锌彩涂板的质量。
**氟碳彩钢板报价-正品氟碳彩钢板哪家专业-正品氟碳彩钢板哪家好-哪里有卖氟碳彩钢板批发
我要给“氟碳彩钢板供应商”留言
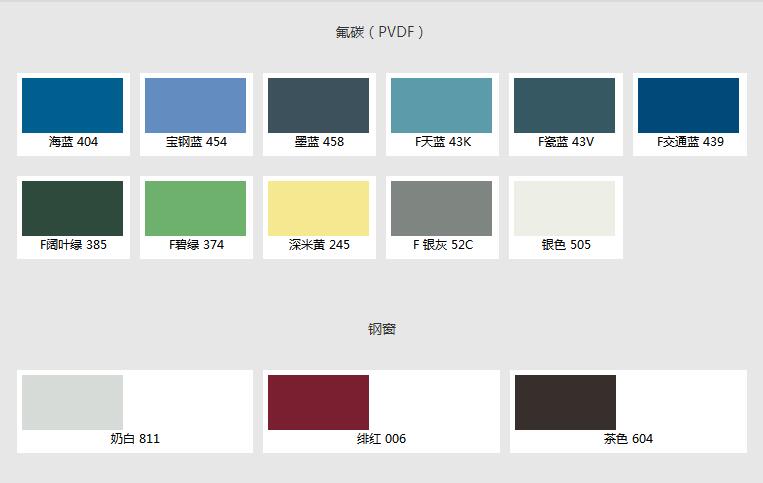
高分子柔性背板特指一类以高分子材料为主体经过多层复合、涂覆、共挤等工艺成卷制成的背板,*1代高分子柔性背板以 TPT、KPK、TPE(一面干式复合PVF材料,另一面复合 PE 等烯烃类或改性的热塑性)、KPE(一面干式复合PVDF,另一面复合PE等烯烃类或改性的热塑性材料)含氟复合型背板为代表;因PE 等烯烃类或改性的热塑性材料仅是从粘结性、低成本考量的短期环境应用材料,故目前主流过渡到一面涂覆一面复合、双面涂覆的双面含氟背板,代表结构类型有 XFB和 FFC,即往*2代背板方向发展,XFB 结构背板所用氟膜主要为PVF和PVDF膜,PVDF 膜随着国内制膜技术的发展,未来2~3年有大规模取代的趋势;PET 结构背板因其经济性,逐步从一代技术的多层复合PET过渡为 AB(A和B 2种或以上改性PET类材料共挤、共混等工艺)结构共挤PET技术,消除了复合PET的2个刚性界面粘结*失效的短板,提升了 PET 结构背板的耐湿热 UV 循环的综合性能,可以在温和环境的分布式电站中应用,同时降低了成本。 当前高分子柔性背板的四大主流结构 XFB、FFC、XPE、PET 的技术路线如图 4 所示。
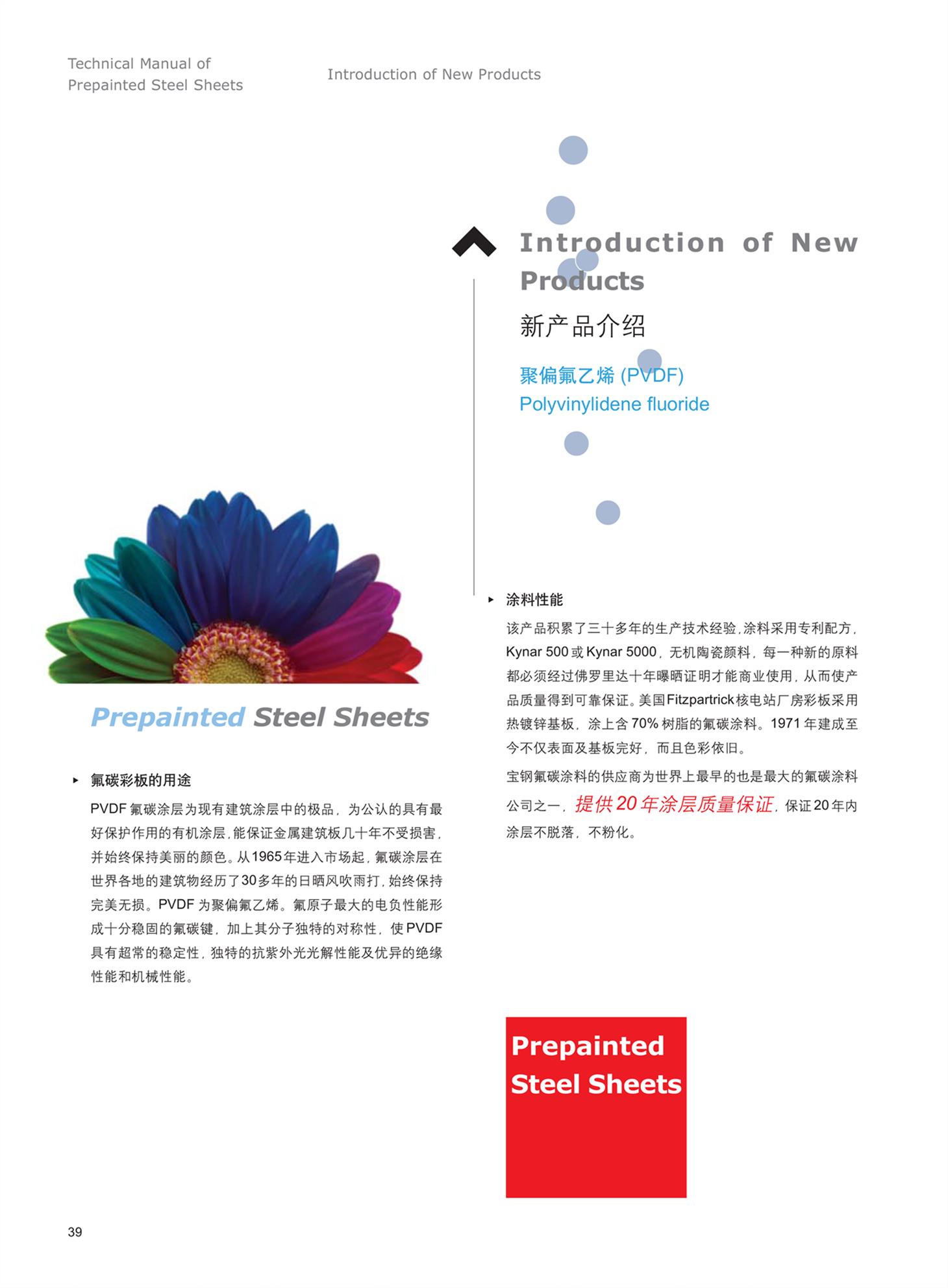
2.2 背板应用创新
一直以来,太阳能背板材料主流是以PET为基膜的多层高分子材料,PET 基膜作为应用较广的绝缘材料,以其优异的性价比在背板材料中作为骨架支撑,发挥了重要的绝缘和阻隔作用。 PET 材料作为背面骨架由来已久,经历大量的研究改进和户外验证后,已经形成了太阳背板**基膜 PET 材料。当然,研究者同时也提出了很多替代性材料,如业内 CSI、Trina 等接到反馈,某国外背板企业提出并实施用尼龙(PA)材料作为背板主体,但经过户外实践发现其具有开裂、发霉、组件发电可靠性等一系列外观和性能问题,这一过渡创新也让行业企业付出了巨大的代价,同时该背板企业及采用类似技术的企业也随之走入了窘境。 当然,创新和颠覆在太阳能光伏领域一直上演,很多创新都带来积极的价值,特别是改良型创新。随着电池效率的不断提升和光伏应用领域的不断拓展,光伏组件封装方式需根据电池的设计和光伏应用领域的需求进行创新,随之而来的各类功能型背板、IBC 背板、双面发电背板等创新背板产品大量涌现,如使用玻璃作为背板和高分子柔性涂氟透明背板的双面透光组件在建筑幕墙、农业大棚等领域得以应用。在以玻璃为背板的非透光双玻组件中,创新地应用了白色 EVA 等封装材料。以玻璃背板 白色EVA 组合替代高分子柔性白色背板,其白色 EVA 的耐候性和材料自身与组合的可靠性还需大量验证,同时因其组合材料成本低,也给传统封装方式的材料带来了巨大的挑战。因而,氟碳涂料涂氟型背板在与传统复合型背板竞争的同时,需不断提高自身功能性,以应对创新型背板材料的竞争。
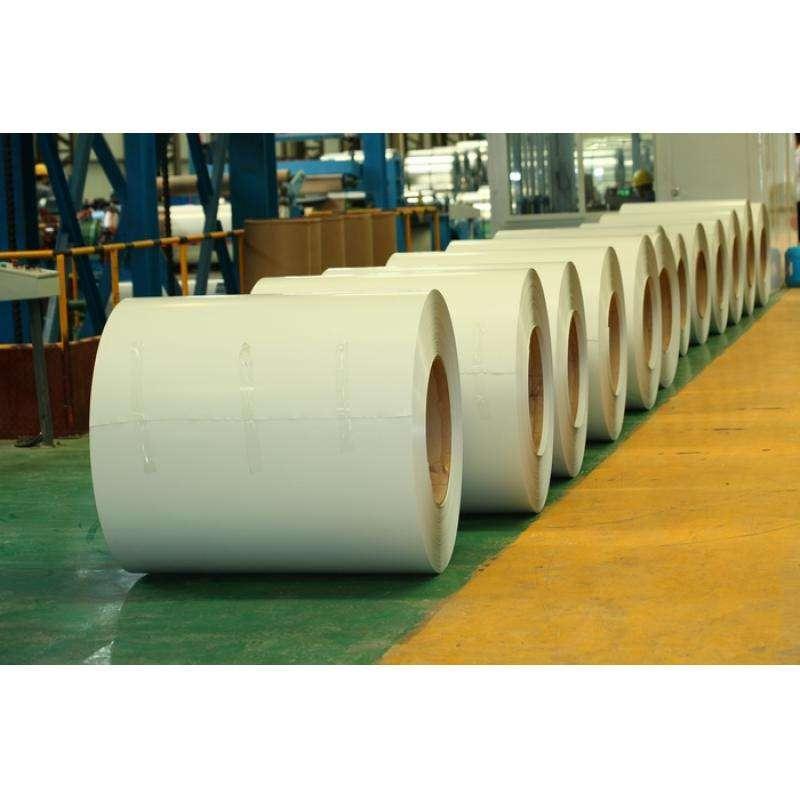
针对在湿热海洋环境下长期服役的铁路混凝土,设计了表面氟碳涂层成套体系,明确了涂层体系应用技术要求,在此基础上规范了施工措施并完善了质量评价体系,实现了涂层防护成套技术在相应工况下的成功应用。效益分析表明,涂层技术的应用降低了铁路混凝土的全寿命期维修费用,兼具环保和社会效益。
关键词 材料工程;铁路混凝土;氟碳涂层;应用技术;海洋环境;耐久性
随着我国对海洋开发规模的不断扩大,各类码头、跨海大桥、人工岛等海洋工程基础设施的建设数量正在逐渐增加。钢筋混凝土由于具有易浇注、耐冲击、耐磨等优良性能以及较低的工程造价,成为进行此类设施建设的可以选择形式。但钢筋混凝土在海洋环境下服役时面临着较严重的钢筋锈蚀等腐蚀问题,易导致结构开裂、失效,缩短结构使用寿命[1]。为保证安全服役,必须对已发生腐蚀的结构进行修复,但技术难度与所需资金均十分巨大。因此,人们对处于严重腐蚀环境下的钢筋混凝土越来越多地采取事前防护措施以提升其耐久性,从而降低全寿命周期的成本[2-3]。
海南省处于典型的高温、高湿、强腐蚀等多腐蚀因素耦合作用的海洋环境下,其区域内钢筋混凝土的腐蚀问题更为**,对效果显著、实施简便、作用持久的混凝土耐久性提升技术措施的需求更加迫切。在诸多技术措施中,混凝土表面涂层技术较为简单有效,不仅可以应用到新建结构上,还可以应用于已有结构的修复[4-8]。本文主要介绍成功应用于新建海南西环铁路提升混凝土耐久性的表面氟碳防腐蚀涂层技术。
1 工程概况
新建海南西环铁路始于既有西环铁路海口站,终于三亚站,线路走向沿海南西部沿海地段,正线全长345 km,设计时速200 km,为I级双线铁路。在西环铁路中段,位于海南省儋州市与昌江县境内的珠碧江双线特大桥全长 3 991 m,桥位与北部湾入海口不足5 km。由于海水倒灌影响,环境腐蚀作用异常严重,其中,氯盐环境的作用等级为L3,化学侵蚀环境的作用等级为H4,盐晶结晶破坏环境的作用等级为Y4,并存在大于Y4等级的高硫酸盐含量的较端严重腐蚀环境,必须对相应环境下的混凝土结构进行防腐蚀强化处理,提升混凝土耐久性。
-/gjdfhe/-
http://shzcsy.cn.b2b168.com